1) Unique classical polishing method
Although the magnetorheological fluid polishing method is thought to be a promising way to make the extra lower roughness optical surfaces, but its high-cost and low producing rate makes it unpractical in industrial applications, therefore most of the super-polished optics are made from the classical polishing method. A unique processing of classical polishing are developed to make the super-polished optics, the pitch plate is used as the polishing module, <1Å roughness can be obtained by our polishing art. The testing show that our substrates and mirrors works well in the laser gyro system.
2) Roughness measurement
For the primary scattering test we use the green laser of 25mW and 40mW, the scattering point can be found by watching the reflection laser light from the optics surfaces, this is easy and fast, which is used as the primary test of surface roughness.For the final test of the roughness or scattering test, the Atom Force Microscope (AFM) of Bruker company is used to measure the final roughness of the polished optics. Please see the following picture get from the AFM measuring system.
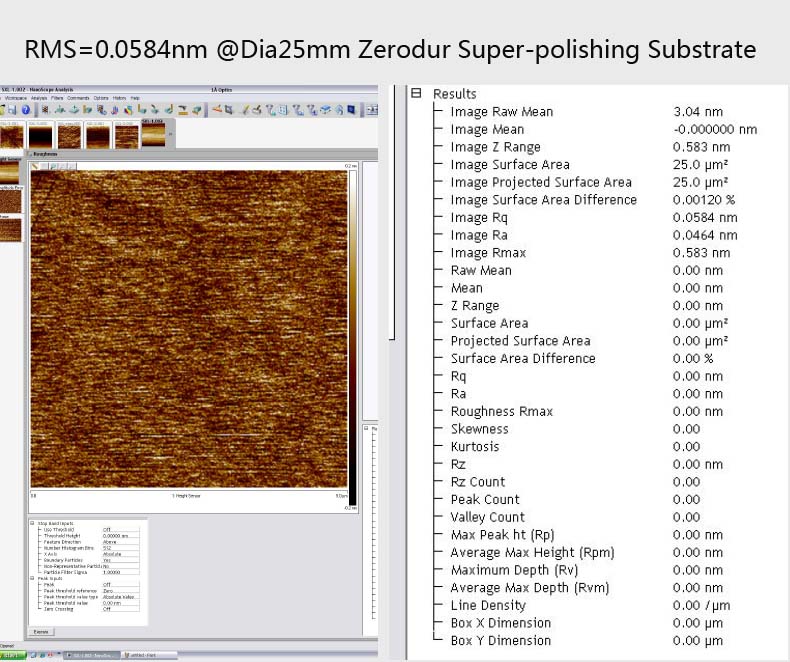
3) Flatness Measuring
The Zygo Lambda2000 series Module GPIXP-D6” is used to measure the final flatness of the polished surfaces. Please see the following diagram of the measuring.
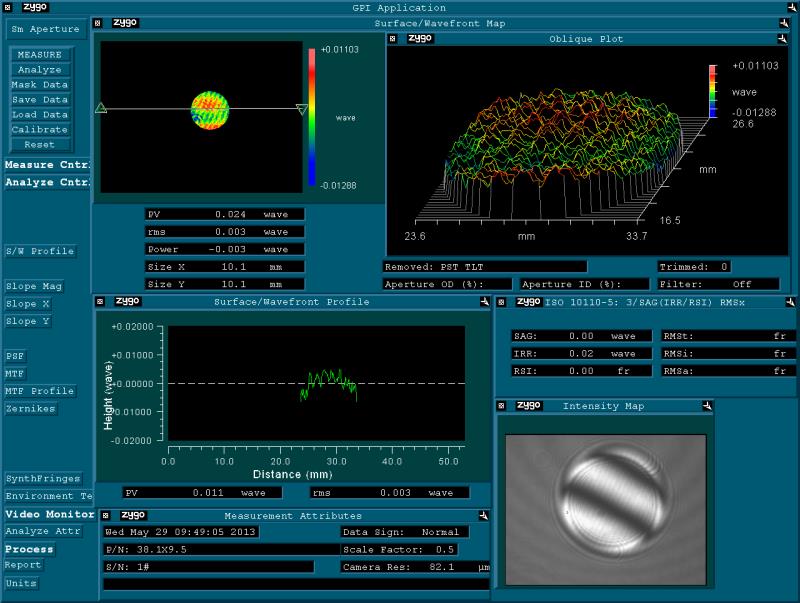
4) Coating Testing
The final processing of coating is also critical for the laser gyro mirrors, low absorption and low scattering loss is required, the Total Integrated Scattering or TIS is measured to evaluate the surface loss of the mirrors.
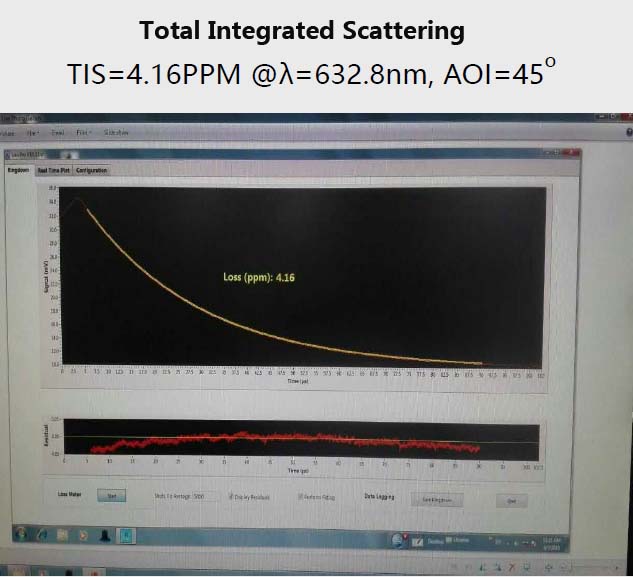
Specifications of the ring laser gyros
Substrate Materials
|
Zerodur Glass, Fused Silca
|
Diameters (mm)
|
F12.5, F19.05, F25
|
Surface Roughness RMS
|
<0.1nm
|
Total Integrated Scattering (TIS)
|
5ppm
|
Surface Quality
|
10/5 S/D; 0/0 at central area
|
Flatness
|
<Lambda/20 @ 633nm
|
Note: the customized specifications is available upon request.